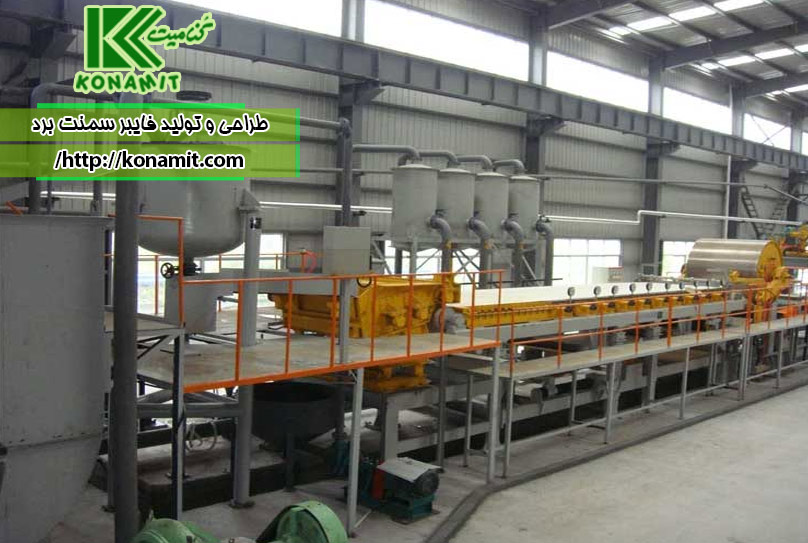
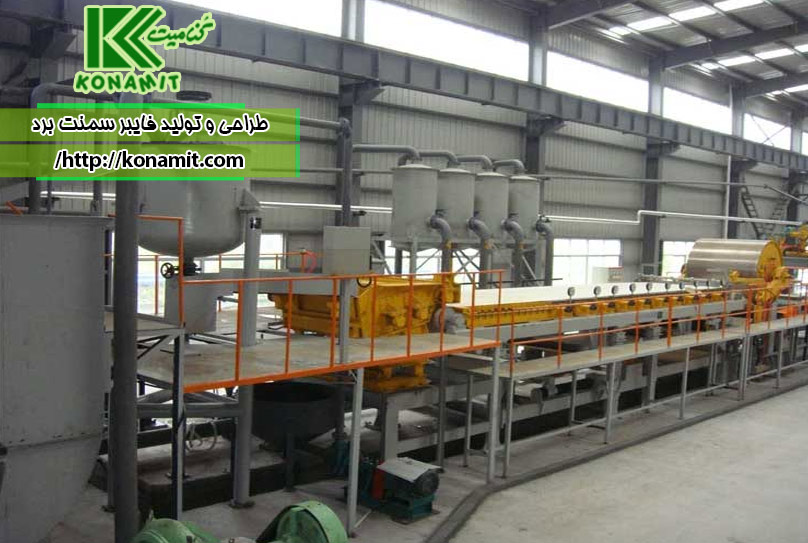
فایبر سمنت برد و تاریخچه آن : یکی از مصالحی که همواره مورد نیاز و احتیاج به مصالحی به شکل صفحه میباشد در گذشته این نیاز را با مصالحی مثل چوب تامین میکردند که در حال حاضر از ورق های گچی ، فولادی، پلاستیکی و … استفاده میکنند که هر کدام از ان ها عیب ها و مضرات خود را دارند.
حدود ۱۱۰سال پیش صفحات سیمانی با استفاده از آزبست تولید شدند اما به دلیل سرطان زا بودن ازبست در صنعت ساختمان کنار گذاشته شد و بجای آن از صفحات سیمانی چوب و… استفاده شد.
( آزبست، پنبه نسوز یا پنبه کوهی که در علم زمین شناسی یک کانی سیلیکاتی حاصل از ماگما و در واقع نوعی سنگ آذرین درونی میباشد. و بطور کلی نام گروهی از ترکیبهای معدنی منیزیم و سیلیسیم است که بیشتر در طبیعت به صورت الیاف معدنی و سنگ یافت میگردد. این مواد به خاطر مقاومت زیادی که در برابر آتش و گرما دارند به عنوان ماده نسوز استفاده میشوند.
گاها به این ماده پشم شیشه نیز میگویند. در ساختار پنبه کوهی یا پنبه نسوز، عناصری مانند سیلیس، منیزیوم و آهن وجود دارد. پنبه کوهی در طبیعت به رنگهای سفید، قهوهای و آبی به چشم میخورد. این ماده سرطان زا و استفاده آن در اروپا و آمریکا ممنوع میباشد.)
فایبر سمنت برد چیست ، تاریخچه فایبرسمنت برد
در سالهای بعد از صفحات سیمانی با الیاف سلولوزی با اسم فایبر سمنت برد تولید شدند که بعد از گسترش و محبوبیت آن، برایش استاندارد های بین المللی تدوین گردید. یکی از بهترین نوع مصالح موجود برای پوشش دیوار و کف و … صفحات سیمانی فایبر سمنت برد میباشند. این صفحات برای ساخت و ساز خشک و سیمانی در تمامی ساختمان هایی که با اسکلت فلزی و بتنی ساخته شده اند برای پارتیشن بندی و پوشش دیوار داخلی و سقف و کف استفاده میشوند. و در ساختمان هایی که با سازه فلزی lsf ساخته شده باشند بهترین گزینه باری استفاده صفحات فایبر سمنت است.
فایبر سمنت برد برای کجا مناسب است؟
- نمای ساختمان
- پوشش های داخلی ساختمان
- برای دکورسازی
- زیرسازی کاشی و سرامیک
- سقف کاذب
- محافظت سازه در برابر حریق
- ساخت مبلمان و دکوراسیون
- دیوار محوطه و پرچین
- تاریخچه ساخت فایبر سمنت
در سال ۱۸۹۰ لودویک هات چک برای ساخت مقواهای با گرماژ بیش از ۸۰ گرم و مقوای چند لایه ماشین اختراع نمود که بنام ماشین مقوا سازی هات چک نام گذاری شد و می توانست مقواهائی با گرماژ بالا حدود ۲۰۰ تا ۳۰۰ گرم تولید نماید .
توضیح اینکه در کاغذ و مقوا سازی سعی براین است که جهت الیاف در جهت حرکت ماشین باشد تا بتواند از یک طرف دارای مقاومت خوبی باشند .
از این تکنولوژی بعد ها در ساخت صفحات سیمان و آزبست فایبر سمنت آزبستی استفاده قرار گرفته که میتوانست ورقه های تا ضخامت ۸ میلیمتر تولید نماید زیرا در آزمایشات انجام شده برای ساخت ورقه هائی با الیاف مدول بالا مانند فولاد ، شیشه ، کربن و کولار و الیاف مدول پایین مصنوعی مانند نایلون پروپیلن و الیاف طبیعی مانند سلولز و کنف بیشترین مقاومت و کیفیت را بعلت ترکیبات شیمیای آزبست و سیمان ترکیب آزبست و سیمان در این نوع فایبرسمنت مورد استفاده قرار گرفت ، علیرغم مشخص شدن سرطانزا بودن آزبست تا سالهای ۱۹۷۰ و تا آواخر دهه ۱۸۹۰ میلادی که فناوری جدیدی براساس تکنولوژی جدید اختراع شده تولید سیمان آزبست ادامه داشت .
تولید فایبر سمنت برد
پس از آن استفاده از آزبست در کشورهای پیشرفته ممنوع گردید و همچنین در سالهای اخیر در ایران هم ساخت فایبر سمنت ترکیبی از سیمان آزبست ممنوع گردید . به همین علت سازندگان با سابقه این محصول در ایران مانند شرکت های ایرانیت ، فارسیت ، پرسیت ، شمالیت ….. تعطیل شدند زیرا ماشین خط تولید هات چک قادر به ساخت ورقه های با کیفیت مناسب با الیاف غیر آزبستی رابرای تولید صفحات فایبر سمنت ندارد و همانگونه که ذکر شد واکنش بسیار خوب سیمان و الیاف آزبستی که فوق العاده خوب و سریع می باشد امکان استفاده از این ماشین را برای تولید فایبر سمنت الیاف آز بست و سیمان ممکن می سازد .
در حالی که برای استفاده از الیاف غیر آزبستی برای تولید فایبر سمنت برد می بایست از روش های جدید و ماشین آلات با طراحی خاص استفاده گردد و به همین علت کارخانجات و شرکتهای نامبرده در ایران پس از ۴۰ سال تولید یکی پس از دیگری مجبور به تعطیلی شدند .
البته در همین حال کشورهای پیش رفته دانش فنی خود را تا سالها در اختیار کشورهای جهان سوم قرار نمی دهند زیرا باعث ایجاد روقبای تازه خواهد شد حتی فروش دانش فنی را آنقدر گران تعیین می کند که برای روقبا خرید آن بصرفه نمی باشد در نتیجه آنها می توانند بدون رقیب به تولید فایبرسمنت بدون آزبست اقدام نمایند .
و سعی نمودن که این تکنولوژی قدیمی را ( خط تولید هات چک ) به کشورهای فاقد تکنولوژی صادر نمایند و با افزودن ماشین آلات جدیدی مانند اتوکلاو اقدام به صادر نمودن این خطوط تولید که در انباره ای آنها باقی مانده بود با این استدلال که در مصرف سیمان صرفه جوی شده و با افزودن آهک و ماسه سیلیسی تولیداتی در حد جهان سوم بنام کارخانه فایبرسمنت ارائه دهند .
طراحی و تولید فایبر سمنت برد دارای استاندارد های خاصی می باشد که شرکت کنامیت توانسته است انواع فایبرسمنت در قالب فایبرسمنت طرح چوب ، فایبرسمنت ساده ، فایبرسمنت طرح آجری و فایبرسمنت رنگی را تولید نماید. نمای فایبر سمنت برد یکی بهترین و لوکس ترین نما ها در جهان محسوب می شود.
مشکلات تولید فایبرسمنت :
در این روش بعلت ناهموژن بودن جهت الیاف در دو طرف ، فایبر سمنت غیر یکنواخت در جهت طولی و عرضی به وجود می آید .
در صورت استفاده زیاد از الیاف بعلت لایه لایه بودن مواد ماده چسبنده در آن کم شده و احتمال متورق شدن صفحات فایبر سمنت را ایجاد می کند و در صورت کاهش الیاف صفحات فایبر سمنت ترد و شکننده شده و قابلیت انعطاف بسیار کمی دارد .
بعلت جمع شدن لایه های سیمان و الیاف روی یک استوانه بنام درام امکان تولید ضخامت های بالای ۸ میلیمتر با ضخامت های مناسب تقریبا غیر ممکن می باشد زیرا شعاع اولین لایه پیچیده شده روی درام با شعاع آخرین لایه بیشتر از ۸ میلیمتر اختلاف دارد و در نتیجه طول آنها ۱۴ * ۸ حدود ۲۵ میلیمتر بیشتر است و در نتیجه وقتی به صورت ورق در می آید چین خوردگی در آنها در می آین و چسبندگی بین صفحات و در نتیجه مقاومت بررشی آن بشدت کاهش پیدا می کند .
لیکن در کشورهای جهان سوم که دارای تولیدات اندک سیمان می باشند و قیمت سیمان بسیار گران است اقدام به ساخت ماشین های با تکنولوژی بیش از یک قرن پیش هات چک می گردد و توجیه آنها قیمت ارزانتر با استفاده از آهک و سیلیس( این ترکیب مقاومت بسیار کمی نسبت به سیمان دارد) می باشد که باید توسط اتوکلاو این ترکیب انجام پذیرد تا قیمت تمام شده کاهش یابد .
روش نوین تولید فایبر سمنت :
واحد تحقیق و توسعه شرکت رزین چوب راش ( رزین فیبر) پس از ۴ سال کار مطلعاتی ، تحقیقاتی و آزمایشگاهی با کسب جدیترین و علمی ترین روشهای ساخت موفق به تولید فایبر سمنت بدون آزبست با کیفیت فوق العاده مطلوب گردید .
آماده سازی الیاف :
در این روش با استفاده از یک سیستم پالایش و یکنواخت سازی الیاف ویژه فایبرسمنت انجام میشود . زیرا الیاف در مرحله اول در درون هیدرو پالپر ممکن است هنوز دارای قطعات باز نشده بصورت تکه های ریز با کاغذ باقی مانده باشند با استفاده از یک ماشین الیاف باز شده از سایر الیاف کاملاً باز نشده جداسازی می گردد سپس با عبور از یک الک ویژه میکرونی الیاف کوتاه شده و بریده شده هنگام بازیافت کاغذ از آنها جدا می گردد و الیاف با طول معیین برای تولید فایبر سمنت به مخزن الیاف وارد می شود ( که با کانسرات معیینی نگهداری می گردد )
روش اختلاط :
با توجه به معین بودن کانسترات وزن معینی از ان توسط کنترل کننده های plc جهت وارد شدن به میکسر ویژه توزین می گردد و به همین صورت سیمان نیز از سیلوی بزرگ به مخزن توزین وارد شده سپس به داخل میکسرهای خاص که جهت اختلاط الیاف سلولز و سیمان ساخته شده داخل می شود این میکسرها به هیچ وجه به میکسرهای متعارف بتون سازی مشابه نمی باشد و طراحی خاص جهت اختلاط و هموژن کردن الیاف سلولز و سیمان به هدف ساخت فایبر سمنت برد می باشد.
ساخت تشک اولیه فایبر سمنت برد
براساس ضخامت مورد نظر تولید فایبر سمنت این مخلوط به داخلی ماشین آبگیری اولیه وارد می شود نحوه ورد این ترکیب به شکلی می باشد که پراکندگی الیاف را در جهات مختلف تعیین می کند و در نتیجه قطعه ساخته شده یک ماده ایزوتراپیک یا هم سو برابر می باشد زیرا الیاف در تمامی جها ت بصورت یکنواخت پراکنده و توزیع می گردد ( فایبر سمنت باید از ماده هموژن ساخته شده باشد )
پرسکاری و مستحکم سازی فایبرسمنت برد :
پس از این مرحله تشک اولیه جهت ساخت فایبرسمنت برد و ایجاد مقاومت ، دانسیته مناسب و آبگیری به داخل یک پرس بزرگ با ظرفیت ۵۰۰۰ تن وارد می شود در این پرس بعلت فشار بسیار زیاد آبگیری کامل انجام شده و نفوذ آب به داخل دانه های سیمان تسریع می گردد با توجه به فشار سنگین پرس که بالغ بر ۷۰ کیلوگرم بر سانتیمتر مربع می باشد ژل تشکیل شده سیمان به داخل الیاف سلولز نفوذ کرده و سلولز و مواد سیمانی بصورت یکپارچه در می آید در این مرحله می توان با قالبهای متنوع که تشک روی آن قرار می گیرد شکل پذیری رویه های با اشکال مناسب ، زیبا و مختلف در یک طرف فایبرسمنت برد ایجاد گردد .
بنابراین در این روش قدرت مانور برای ساخت انواع و اقسام رویه ها با برجستگی های مناسب در فایبر سمنت برد ایجاد می گردد در این روش امکان ساخت انواع نماهای متنوع مانند نمای آجری ، نمای چوب ، نمای سنگی و طرح های اسلیمی برای صفحات فایبر سمنت امکان پذیر می باشد .
عمل آوری :
پس از خروج از پرس این قطعات به مدت ۳ روز که زمان هیدراتا سیون سیمان می باشد در درون آب قرار می گیرند بعلت فشار بالای پرس و نفوذ آب به درون دانه های سیمان در عرض این مدت فایبرسمنت به مقاومت بالائی می رسد و سپس برای برش کاری و اندازه بری به داخل دستگاهای اتوماتیک برش کاری انتقال پیدا می کند .
خشک کردن فایبر سمنت برد :
خشک کردن قطعات ضخیم توسط هوا بعلت آنکه خشک شدن از رویه انجام می گیرد و باید زمان مناسب نفوذ آب از وسط فایبرسمنت به رویه حفظ گردد تا در اثر اختلاف رطوبت در وسط و سطح فایبرسمنت باعث ایجاد تنشهای داخلی و در نتیجه احتمال ترکهای میکروسکپی نگردد درصورتیکه این عمل در زمان کوتاه و با حرارت بالا انجام شود این تنشها بسیار زیاد خواهد بود و باعث کاهش مقاومت نهائی فایبر سمنت می گردد براساس محاسبات انجام شده زمان خشک کردن در کوره های بستگی به ضخامت فایبرسمنت از ۲۰ ساعت تا ۴۸ ساعت انجام میگیرد که اجرای این عمل توسط ماشین های الکترونیکی برنامه ریزی شده وکنترل می گردد .
خلاصه روش مناسب و تکنولژی جدید علمی جهت ساخت فایبرسمنت برد بدون آزبست
تهیه الیاف هموژن با طول مناسب جهت مصرف در فایبر سمنت
اختلاط کامل و مناسب سیمان و الیاف توسط میکسرهای ویژه برای تولید فایبرسمنت
تشکیل تشک مناسب به وسیله ماشین های آبگیری که می توانند الیاف را در جهات مختلف پراکنده نموده و فایبر سمنت برد با مقاومت یکنواخت در جهت طولی و عرضی تولید نماید .
پرس با فشار بالا جهت آبگیری و نفوذ سریع آب به داخل دانه های سیمان و تشکیل سریع ژل سیمان و نفوذ ژل به داخل الیاف برای استحکام و چسبندگی سیمان انجام میگردد .
زمان لازم جهت هیدراتاسیون کامل سیمان و پیوند مناسب الیاف و سیمان در ساخت فایبر سمنت برد در آب .
برنامه مناسب برای خشک نمودن با حرارت و زمان مناسب و طولانی و متناسب با ضخامت فایبر سمنت تا تنش های خشک شدن آسیبی به مقاومت فایبرسمنت نرساند .
بعلت انعطاف پذیری خط تولید امکان ساخت طرح های زیبا برای نما سازی با فایبر سمنت برد با روش نوین امکان پذیر می باشد
آیا می دانید فایبرسمنت برد چه مزایایی در ساخت و ساز دارد؟
مطمئن باشید که سایدینگ فایبر سمنت، نمای خانه شما را متحول خواهد کرد. این ماده چندکاره، یک سرمایهگذاری هوشمندانه است زیرا ویژگیهای مقاومی را به همراه دارد.
مراقبت آسان: بدون نیاز به جلاکاری و درزگیری، یک نظافت ساده و مرتب با شیلنگ باغبانی یا آب فشاری برای رفع چرک و کثیفی کفایت میکند. برای برطرف کردن چرکها و سیاهیهای چسبنده و ماندگار، از رنگ یا روغن جلادهنده استفاده کنید.
مقاومت در برابر شرایط آب و هوایی: آیا فایبر سمنت برد در محیط های خاص قابل استفاده می باشد؟
این محصول در کنار مقاومت در برابر باران، افزایش زیاد دما، اشعه فرابنفش و باد، ضد حریق نیز میباشد. این خصلتها، امکان نصب فایبر سمنت را در هر نوع شرایط آب و هوایی، فراهم میکنند.
پایایی: این ماده در مقابل خراش، لبپریدگی، پوستهپوسته شدن، ترکخوردگی و تاب برداشتن مقاومت میکند. همچنین، ضد حشره است زیرا حاوی هیچ ماده غذایی برای حشراتی چون موریانه نیست.
استقامت ابعادی: این روکش در اثر تغییر دما یا هوا، دچار آب رفتگی یا آماس نمیشود.
کارایی: فایبرسمنت، انتخابی مناسب برای افرادی است که میخواهند؛ سایدینگ را بهگونهای رنگ بزنند که رنگ را به خوبی به خود بگیرد. تجدید پوشش فایبر سمنت، امری بسیار راحت است.
برای اجرا و نوسازی سریع سایدینگ فایبر سمنت این نکات را رعایت کنید
بعد از انتخاب مدل موردپسندتان، زمان خرید سر میرسد. توصیه میشود؛ کمی بیشتر از مقدار محاسبه شده، سفارش دهید چون ممکن است حین حملونقل آسیب ببیند. میزان خسارت مجاز برای این ماده، ۵ درصد است. البته مقداری هم به عنوان خسارات ناشی از تخلیه محصول در نظر بگیرید که این مقدار گارانتی نمیشود.
بهتر است که پروسه نصب را به یک فرد کارکشته بسپارید چون نصب فایبر سمنت، معمولی نیست.
فضایی که قرار است روکش شود؛ باید به خوبی هواگیری شود تا باعث دمیدن گردوخاک نشود زیرا در این صورت، سایدینگ فایبر سمنت، بریدهبریده میشود.
کاهش وزن ساختمان با فایبر سمنت برد
سبک سازی یکی از مباحث نوین در علم ساختمان است که روز به روز در حال گسترش و پیشرفت می باشد.
این فناوری عبارتست از کاهش وزن تمام شده ساختمان با استفاده از تکنیک های نوین ساخت مصالح جدید و بهینه سازی روش های اجرا کاهش وزن ساختمان علاوه بر صرفه جویی در هزینه زمان و انرژی زیان های ناشی از حوادث طبیعی مانند زلزله را کاهش داده و صدمات ناشی از وزن زیاد ساختمان را به حداقل می رساند.
برای بکارگیری تکنیک های سبک سازی نخست باید به مسئله اول علل سنگین شدن وزن ساختمان توجه کافی شود؛ پس از شناخت این علل و عوامل باید جهت حذف یا به حداقل رساندن تاثیر آنها و وزن تمام شده ساختمان تلاش نمود.
روش های سبک سازی ساختمان بطور عمده به دو دسته تقسیم میگردند :
۱) سبک کردن اجزای باربر ساختمان
۲) سبک کردن سازه ساختمان
بخش عمده ای از مباحث مربوط به سبک سازی و تکنیک های رایج در مورد دستیابی به وزن مناسب ساختمانی را در بر میگیرد که شامل: شناخت مصالح سبک رایج در صنعت ساختمان (در داخل و خاج کشور)وتکنولوژی استفاده از آنها, معیار های ارزیابی میزان کارایی این مصالح بعنوان مصالح سبک و میزان تاثیر به کار گیری مصالح نو در کاهش وزن ساختمان هزینه و زمان مورد نیاز اجرای یک ساختمان.
تعریف مصالح سبک: مصالح سبک به مصالحی اطلاق می شود که وزن مخصوص آن ها از نمونه های مشابه کمتر بوده و استفاده از آنها به کاهش وزن کلی ساختمان بیانجامد.